With photovoltaic plants having the highest installation rate of all power sources in the last five years, the need for monitoring these plants is essential in maintaining power output and life expectancy. Are the current industry standard utility-scale monitoring systems enough to appropriately detect possible faults that could lead to power failure? A team at the Florida Solar Energy Center has spent the last five years studying the value proposition of high-resolution monitoring systems (HRMS) to determine its effectiveness on levelized cost of energy (LCOE) reduction.
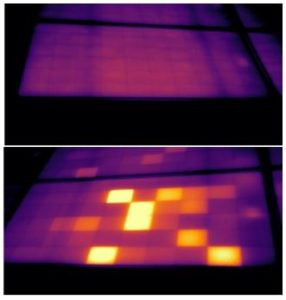
spots when string was operated at MPPT. But, the same module showed signs of checkered pattern hotspots when operated at off-MPP.
“The project’s purpose is studying the value of monitoring the modules and strings in detecting the photovoltaic (PV) faults and its impact on LCOE,” Manjunath Matam, post-doctoral scholar at FSEC and project lead, says. “The PV modules and strings are all connected to the inverter and it is hard to detect the faults using the inverter data. Sometimes, the faults never get detected and cause huge power losses in the long run.”
So how does this U.S. Department of Energy-sponsored project benefit PV plant owners and investors? “The PV plant owners, investors, utility companies, stakeholders have no idea whether installing the HRMS equipment to monitor the modules and strings will add value, produce more power and generate revenue, or if it will just be an additional expenditure,” Matam says. “Our project, through its simulation, hardware, indoor and outdoor experiments, has observed that installing the HRMS equipment to monitor the strings will add value and is very beneficial since it can detect the faults, even the low power-loss causing faults, after a reasonable amount of time.”
While installing an HRMS setup is a cost to PV plant owners, it’s value adds up in it’s ability to detect faults in time, reduce losses, and incur more benefits. The project team was able to determine that LCOE analysis confirmed the HRMS is a valuable asset in reducing the LCOE of a PV plant and actually adds economical value to the plant.
“We are quite happy to have completed this project successfully,” Matam says. “We have learned many lessons throughout this long project, particularly from the field perspective. When we worked on the PV plants that lasted ten years in the field, we observed that they pose more problems. For example, something as simple as disconnecting the module MC4 connectors seems to be a challenging task. Another lesson is frequent failure of the blocking diodes that are purchased in the open market, where not many companies are actually producing this product. At times, this would impact the measurements and cause hardware problems.”
“Management of the data is another important lesson we learned in this project,” Matam continues. “The I-V curve data collected from the modules and strings is quite different from the regular data collected from the inverters or metrological stations. We could not store them in the same data structure. Throughout the project, we were able to devise a plan to store them separately.”
More detailed information about this project can be found in the team’s publication: “Best Practices Guide for Utility-Scale PV Monitoring with Intelligent Diagnostics Using String-Level I-V Curves and Machine Learning”.
Further information regarding FSEC and its current projects can be found here.